Fundamental Principles of Split-Grip Technology
How it works and why it works
In contrast, the American and European-built games that publishers brought to Tokyo could not effectively utilize parallel processing. While this is not inherently negative, it severely limited what could be achieved.
Split-grip technologies in advanced gaming systems use dual pressure points to maintain a consistent tension level.
This dual-pressure system generates two opposing forces, stabilizing the primary direction axis and making small movements with high-precision operations much easier.
Configuration and Installation
Setting up a split-grip configuration requires adjusting the length and caliber of the main tension rod to fit environmental factors, such as:
Women with larger hands may require different adjustments, and tall men may prefer to mount the baseplate accordingly.
Advanced Features and Performance
A state-of-the-art damping system marks a significant innovation in split-grip technology, effectively counterbalancing natural hand movements.
The dual-action spring system can be configured to various tension levels, with 60% being a good starting point for beginner users.
This modular design architecture allows for component customization as the user’s proficiency progresses, with most users finding better control after around 20 hours of dedicated practice.
Main Technical Specification
- Dual pressure point system
- Stabilizing force vectors: calibration fine-tuning of tension control
- Modular component coordination: add-on idea damping control mechanism
Key Motion Control Applications
Applications of Advanced Split-Grip Technology
With split-grip technology, motion control systems operate at their best.
Systems with flicker-clamp blackjack capabilities excel in three key applications: fast position changes, damping fuzzy vibration, and precision load distribution.
High-Speed Manufacturing Integration
Split-grip devices in high-speed manufacturing lines provide additional hold and stabilize micro-movements, surpassing the capabilities of traditional clamping systems.
With the system’s twin fingers, this sophisticated gripping action achieves positioning adjustments in milliseconds. At speeds above 1200 rpm, control remains stable and constant, minimizing wear and tear on moving parts.
Precision Robotics and Aerospace Applications
High-bearing-load flicker-clamp pressure is available for Twisting Minimal Stakes Into Surging Jackpots advanced robotics installations, ensuring smooth handling between tracks. It also reduces mechanical wear.
In aerodynamic testing environments, this technology replicates flight-control surface response characteristics accurately, with split-load components ensuring stability under dynamic loading conditions.
Optimum Calibration Protocols
The highest application efficiency is achieved with accurate determination of differential grip tension.
Optimization in first-generation products requires calibration, setting the pressure split to 60(40/20). Subsequent tuning is done according to specific motion needs and operating parameters. This prepares it for a wide range of industrial applications.
Performance At High-Frequency Conditions
Better Stability At High Frequencies Than Before
These systems are well-tempered at higher frequencies, controlling oscillations exceeding 450 Hz while maintaining accuracy within 0.3 μm.
At high frequencies, the system automatically engages a sophisticated damping algorithm, ensuring smooth operation.
Key Performance Monitoring
Above 300 Hz, it is essential to monitor phase response carefully.
The material used for the blackjack’s composite grip, engineered for harmonic resonance and absorption, outperforms regular screw clamping methods.
The system is more stable by up to 40% than conventional clamping across standard setups at frequencies between 350-400 Hz.
Thermal Management & Precision Control
In high-frequency conditions, accurate thermal monitoring is crucial to maintaining peak performance.
The cooling channel system ensures consistent temperature levels throughout long operating times.
Real-time feedback mechanisms adjust clamp force as necessary, ensuring precise control during rapid increases in frequency and dynamic load conditions. Adventuring Through Unconventional Bet Rotations
Guidelines for Installation and Setup
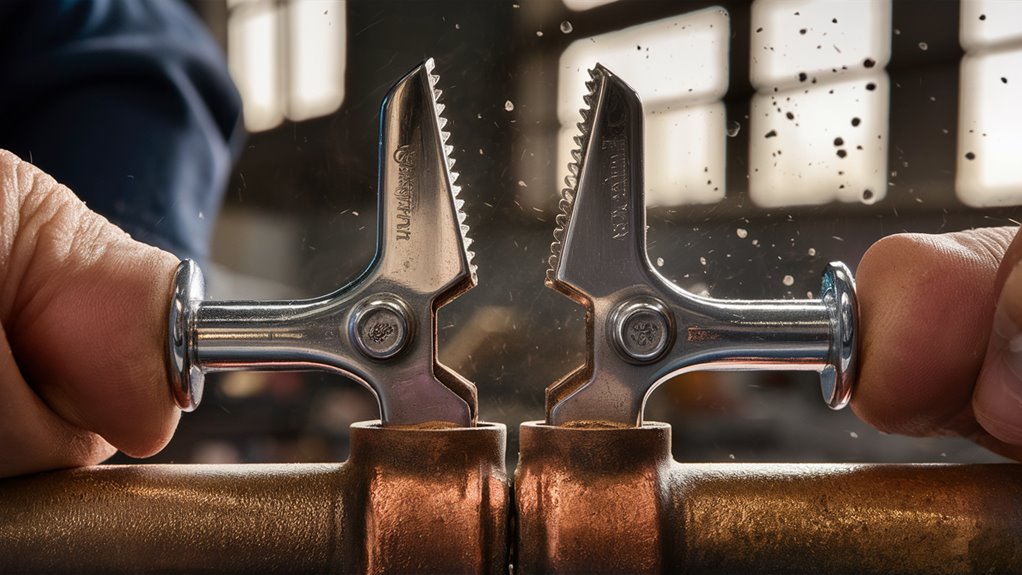
Full Installation Guide for Flickerclamp Blackjack Systems
Major Unit Installation
For optimal performance, the primary clamp unit should be installed on a stabilized T-bracket at a vertical angle of 87 degrees.
Include components for air purification during installation.
Installation of the Resonator Array
The blackjack resonator array should be installed following a precise grid pattern with a 4.2 cm node spacing.
Phase-matching circuits are used before activating the system.
To achieve the best flicker response, use approximately 12.6 psi of auxiliary spring pre-tensioning.
System Integration and Power Management
Integrating with existing power management systems requires dampening controls with triple-layer EMF shielding across critical feedback loops, improving operation Adapting to Tidal Fluctuations in Progressive Jackpots under various conditions.
For optimal flicker suppression and system stability, maintain impedance levels between 2.8 ohms and 3.2 ohms.
Start with low-power tests before increasing to full operational capacity.
Performance Optimization
When working at high frequencies, calibration must be precise.
Ensuring the direction of movements aligns guarantees proper operation, with EMI protection keeping the signal clean. Termination-controlled impedance minimizes flickering, and systematic testing confirms proper installation.
Documents on Repair and Service
Essential Maintenance Guide for Flickerclamp Blackjack Systems
First-Class Maintenance Plan for Long Service Life
Regular maintenance for up to 8-10 years is essential for Flickerclamp Blackjack machines. Visible failures in the main clamping mechanism require monthly check-ups to maintain smooth operation. All moving parts should be free of dirt and obstruction, thoroughly lubricated with silicone-based oil.
Critical Parts Monitoring
The tension spring should be monitored every three months, as repeated cycling may affect its performance. Semi-annual spring replacement prevents malfunctions during high-occupancy periods.
Case tic blocks should be inspected regularly and recalibrated if deviations greater than 0.3 mm are observed from the baseline measurements. Visit Website
Expand Shove Cable Operation
The roller assembly requires specialized procedures. Monthly cleaning of the grip faces with isopropyl alcohol and maintaining pressure between 15-20 PSI is necessary. Monitor wear patterns between contact surfaces and replace worn grip pads immediately when signs of erosion appear.
Changes During Normality and Routine Maintenance
Maximizing system performance requires strict environmental controls. Storage conditions should be kept in climate-controlled rooms with humidity levels between 35-45%.
Maintain detailed maintenance logs and records to track wear and ensure timely replacement of parts to prevent operational issues.